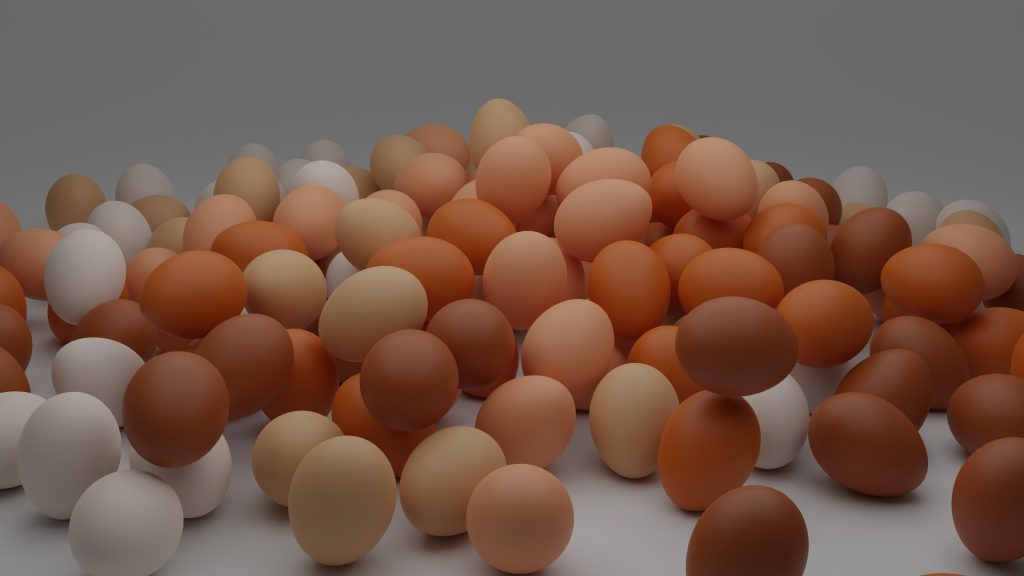
Deviation management is used in many different contexts, for example in quality work, HSE, auditing and internal control. In general, deviations may be that a measure was not 100% implemented, while a more specific example is that 5 units in a production of 100 were defective.
It is important to handle deviations, and i.a. manufacturing companies use dedicated systems or quality systems for this. In such cases, quality and KPI data are often integrated into our business management software as part of a company’s business reporting – something our customers use the system for.
Others use the built-in non-conformance management functionality of our Strategy Orchestrator product. Here it is possible to register different types of deviations and define measures to address the deviations, which is an important part of deviation management.
Of course, there are rich opportunities for reporting discrepancies in various contexts in the product.
In addition to the advantage of deviation management being in the same system where you have goals, strategies, other projects and KPIs, an advantage in our software is that it is possible to look at root causes.
Understanding causal relationships and root causes is essential to be able to define the right measures and avoid deviations.
It is also valuable to see deviations and especially measures to reduce deviations in connection with risk. Our solution includes good functionality for risk, including models for simple and complex risk analysis.
Del på sosiale medier